Простые технологии обработки пластмассы и металла при изготовлении корпусов радиоаппаратуры. УНЧ, часть 6.
Простые технологии обработки пластмассы и металла при изготовлении корпусов радиоаппаратуры. УНЧ, часть 6.
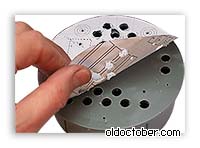
Приближается к завершению постройка моего УНЧ. Посвятил целый божий день корпусным работам и теперь всё готово к окончательной сборке – самому приятному этапу постройки любой самоделки. https://oldoctober.com/
В этой статье я расскажу о нескольких простых приёмах по разметке, сверлению, вырезанию отверстий произвольной формы и другой доработке деталей из пластмассы и металла.
Самые интересные ролики на Youtube
![]() |
![]() |
![]() |
![]() |
Другие статьи о постройке самодельного УНЧ.
Как рассчитать и намотать силовой низкочастотный трансформатор для блока питания УНЧ? FAQ.
Самодельный усилитель и колонки для компьютера из доступных деталей. УНЧ, часть 1.
Техническое задание и сборочный чертёж для самодельного усилителя. УНЧ, часть 2.
Блок питания для усилителя низкой частоты из доступных деталей. УНЧ, часть 3.
Блок электронной регулировки громкости, стереобазы и тембра. УНЧ, часть 4.
Блок оконечных усилителей низкой частоты. УНЧ, часть 5.
Простые технологии обработки пластмассы и металла. УНЧ, часть 6.
Финальная сборка, наладка и испытание. УНЧ, часть 7.
- Где взять пластиковый корпус.
- Несколько слов о материале корпуса, если он не из металла.
- Разметка и обработка деталей из пластмассы и металла.
- Как укоротить канализационную заглушку?
- Описание простого способа выпиливания отверстий произвольной формы в изделиях из пластмассы.
- Вырезание отверстий большого диаметра в листовом материале.
- Сверление отверстий в алюминии и меди.
- Дополнительные материалы к статье.
Где взять пластиковый корпус.
Пластмассовые заготовки для изготовления корпуса можно купить на радиорынке, в магазине по продаже стройматериалов и сантехники или просто воспользоваться какой-нибудь подходящей по размеру пластиковой коробкой.
В «Дополнительных материалах» есть ссылка на справочник с размерами и изображениями готовых корпусов, продающихся на радиорынках.
Несколько слов о материале корпуса, если он не из металла.
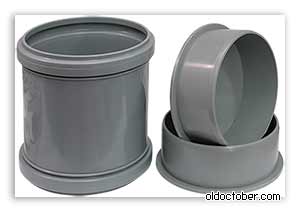
Меня тут некоторые товарищи высмеивают в связи с выбранными заготовками для изготовления корпуса, поэтому я остановлюсь чуть подробнее на причинах этого выбора.
В качестве корпуса для УНЧ и АС я использовал полипропиленовые канализационные трубы. Материал этих труб выгодно отличается от полистирола, из которого изготавливается большинство готовых корпусов. https://oldoctober.com/
Несколько важных отличий полипропилена от полистирола.
- Корпус из полипропилена не деформируется при длительном воздействии температуры до +70ºС и выдерживает в течении 5 минут температуру 95ºС. Полистирол при таких температурах, либо быстро становится хрупким, либо начинает менять форму.
- Полипропилен не боится воздействия агрессивных жидкостей, таких как ацетон, бензин и пр. А случайное попадание нескольких капель подобных жидкостей сразу повреждает поверхность полистиролового корпуса.
- Прочность изделий из полипропилена на порядок выше, чем из полистирола, хотя последний, почему-то, часто называют ударопрочным.
- Есть ещё одно важное отличие этих материалов. Полипропилен не так быстро, как полистирол усыхает, то есть меньше газует. А полистирол через 5-10 лет эксплуатации становится хрупким. Это особенно заметно по всевозможным защёлкам, которые начинают ломаться даже намного раньше этого срока. Что касается полипропилена, то изделия, изготовленные из него, рассчитаны на 50 лет эксплуатации в самых жёстких условиях.
Наверное, можно изготовить корпус и из аналогичных ПВХ (ПолиВинилХлорид) труб, но я подозреваю, что ПВХ не столь стабильный и безопасный материал, как полипропилен. Слишком много опасных для здоровья химикатов используется при его производстве. Один Хлор чего стоит.
Разметка и обработка деталей из пластмассы и металла.
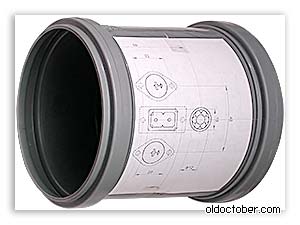
Если Вы подготовили чертёж не на бумаге, то нужный его фрагмент можно просто распечатать на принтере и использовать как шаблон. Если принтер сильно искажает размеры, то нужно ввести поправку при выводе на печать.
Могут возникнуть вопросы в связи с тем, что на цилиндрических поверхностях, разметка по плоскому чертежу может дать существенные погрешности. Да, это так. Поэтому, при вычерчивании проекций цилиндрических поверхностей, нужно вводить поправку.
Для тех, кто не желает долго возиться с пересчётом хорды в длину дуги, предлагаю воспользоваться простыми интерактивными калькуляторами, расположенным на этом сайте www.fxyz.ru.
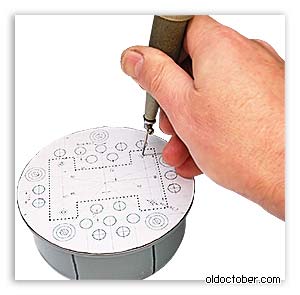
Пластмассовые детали можно разметить при помощи шила.
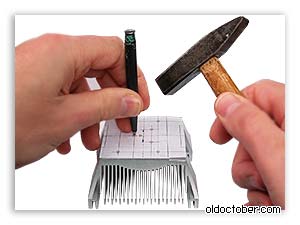
Металлические детали можно разметить при помощи кернера (остро оточенного стального бойка).
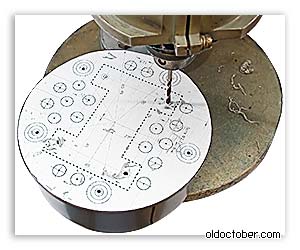
Сверлить отверстия тоже лучше прямо через бумагу чертежа.
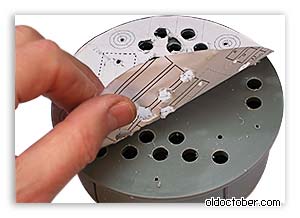
Когда сверловка производится сквозь чертёж, почти невозможно совершить ошибку и перепутать диаметры отверстий.
Как укоротить канализационную заглушку?
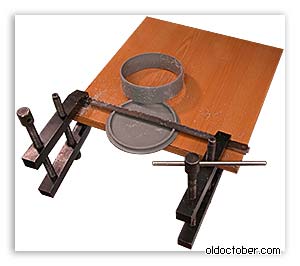
Вот таким способом можно укоратить заглушку, если требуется использовать её в качестве одной из стенок корпуса, а её стыковочная часть мешает другим деталям конструкции.
Прижимаем ножовочное полотно к столу через прокладки необходимой толщины и отпиливаем всё лишнее, двигая заглушку вдоль полотна.
Описание простого способа выпиливания отверстий произвольной формы в изделиях из пластмассы.
Есть старый, испытанный способ проделывания прямоугольных отверстий в пластмассе, путём рассверливания контура по периметру будущего отверстия. Но, этот способ требует разметки и сверления большого количества отверстий. Причём сверлить такие отверстия удобнее на сверлильном станке, который есть не у каждого. Сверление же ручным инструментом может привести к браку. Так, некоторые пластмассы, например, плексиглас можно легко повредить при сверлении даже на сверлильном станке, если неправильно заточить сверло или если во время сверления заготовка неплотно закреплена.
Другой способ предполагает использование лобзика. Но, при выпиливании по пластику, полотно лобзика быстро нагревается и начинает вплавляться в пластмассу. Можно, конечно, наладить водяное охлаждение, но это усложняет работу, да и создаёт много лишней грязи.
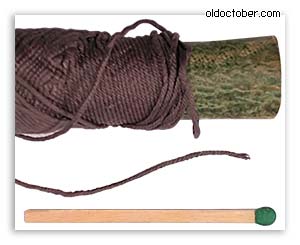
Я же Вам предлагаю технологию, которая лишена всех описанных выше недостатков.
Основой технологии являются обыкновенная суровая хлопчатобумажная нить. Она и исполняет роль «режущего» инструмента. Только, этот инструмент не режет, а плавит пластмассу. Стружка, как таковая не образуется, хотя незначительное количество оплавленного материала может отделиться от заготовки.
Если выполнить разметку по пластмассе чертилкой, то во время прорезки окна нитью, линии разметки можно не разглядеть. Чтобы разметку было хорошо видно, её лучше обвести фломастером или маркером, которым наносят надписи на DVD диски. Если высокая точность не требуется, то разметку можно сразу сделать маркером. Удалить разметку, сделанную маркером, можно клочком бязи (х/б ткани), смоченной в спирте.
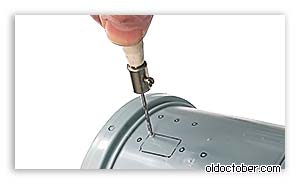
Чтобы начать проплавление контура, придётся просверлить одно единственное отверстие для нити.
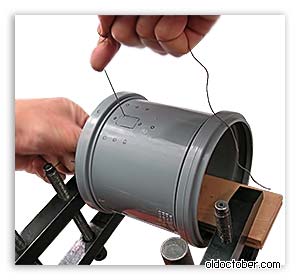
Пластмассовую заготовку следует надёжно закрепить в тисках или прикрутить струбцинами к верстаку.
При выпиливании отверстий в хлипких пластмассовых деталях, вместо тисков, можно использовать помощника.
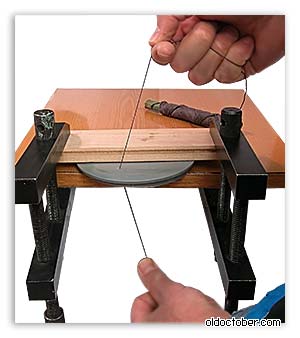
Когда заготовка надёжно закреплена, нужно просунуть нить в отверстие и начать выпиливание по разметке. Конечно, при выпиливании, желательно оставить припуск на окончательную обработку.
Выпиливание нитью требует некоторой сноровки и внимательности. Во время выпиливания нужно всё время поддерживать стабильное натяжение нити и ни в коем случае не прерывать процесс до его окончания. Если всё же требуется прервать процесс, например, для поворота заготовки, то нужно, не прекращая движения, снизить прижим нити к пластмассе. В противном случае, нить может вплавиться в пластмассу и порваться.
Не стоит опасаться применения этой технологии. Попробовав один раз, Вам больше никогда не захочется возвращаться к дрели или лобзику.
Кроме этого, одной катушки ниток хватит на всю жизнь Вам и вашему сыну.
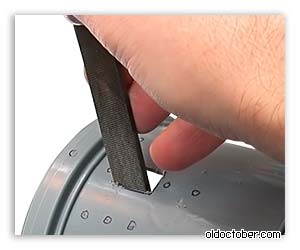
Вырезанное отверстие можно обработать напильником по имеющейся разметке.
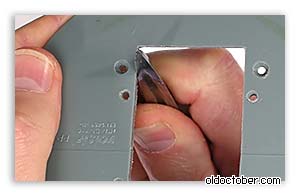
Для более чистой обработки, можно воспользоваться шабером. В качестве шабера подойдёт любой остро отточенный, а затем отполированный инструмент. Хороший шабер можно изготовить из негодного трёхгранного напильника. Если нет возможности заправить напильник, то можно воспользоваться даже скальпелем.
Вырезание отверстий большого диаметра в листовом материале.
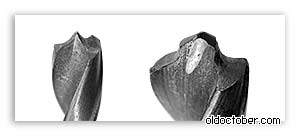
Просверлить отверстие большого размера в тонком листовом материале можно при помощи сверла со специальной заточкой – цапфенбор. Метод не плох, но свёрла большого диаметра недёшевы. Кроме этого, радиолюбитель редко располагает патроном для свёрл больше, чем на 9-12мм, а тем более, конусным шпинделем. А чтобы проточить хвостовик сверла, требуется токарный станок. В тоже время, многие элементы оформления УНЧ требуют сверления отверстий размером 15-20мм
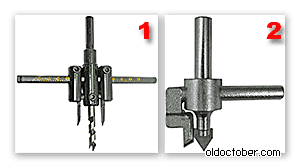
Казалось бы, можно воспользоваться инструментом белеринка. Но, готовые балеринки, либо имеют слишком большое расстояние между резцом и валом (поз.1), либо не годятся для вырезания отверстий в листовых материалах (поз.2).
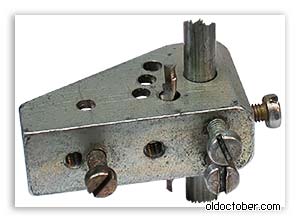
Когда-то, для проделывания отверстий под ламповые панели, я изготовил вот такую балеринку. Она состоит всего из трёх деталей, причём двумя из них могут служить хвостовики от поломанных свёрл.
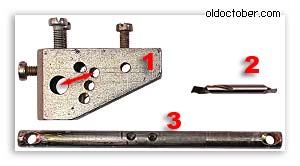
- Угольник – Сталь
- Резец – обломок сверла Ø2,7мм
- Вал – Сталь Ø5мм
В угольнике просверлено насколько отверстий для установки резца. Расстояния между этими отверстиями и центром ведущего вала определяют диаметр вырезаемых дырок. Вместо угольника столь сложной формы можно применить П-образный швеллер небольшого размера или любой другой подходящий по размеру металлический брусок.
Для надёжной фиксации угольника, в вале просверлены неглубокие отверстия, в которые попадают крепёжные винты. Если в качестве вала используется сверло или обломок сверла, то вместо этих отверстий на хвостовике сверла можно проточить лыску на наждачном круге.
И резец, и вал крепятся у угольнику винтами М3.
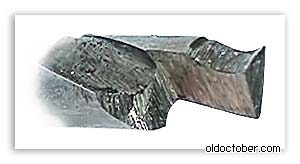
На картинке сильно увеличенная режущая часть резца. В качестве резца использован обломок сверла, заточенный, как обычный резец. В некоторых пределах диаметр прорезаемых отверстий можно регулировать шириной режущей кромки.
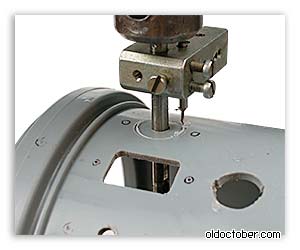
А на этой картинке запечатлён процесс вырезания отверстия в канализационной полипропиленовой трубе.
Описанной здесь балеринкой я вырезал отверстия в алюминиевых сплавах толщиной до 2мм. Для смазки использовал кашицу, изготовленную из хозяйственного мыла и воды.
Бонусом, при вырезании отверстий этой балеринкой, являются большие шайбы М5 правильной формы.
Сверление отверстий в алюминии и меди.
Как не крути, а без металлических деталей при постройке усилителя не обойтись. Как минимум, придётся сверлить отверстия в заготовке радиатора охлаждения микросхем.
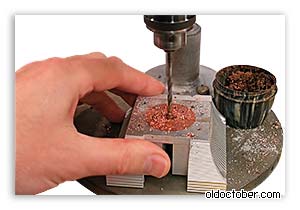
Медь и сплавы алюминия являются довольно вязкими материалами, поэтому, при их обработке, нужно обязательно использовать смазку.
В качестве смазки очень удобно использовать густую кашицу из воды и хозяйственного мыла.
После того, как все отверстия просверлены, заготовку нужно просто промыть водой.
Дополнительные материалы к статье.
Чертежи корпусов с размерами серий «Z» и «KM» (5,6МБ).
caps, снимая фаску, мы уменьшаем площадь соприкосновения корпуса микросхемы с радиатором. Но, с учётом того, что отверстие в корпусе микросхемы больше резьбового отверстия в радиаторе, можно сделать небольшую фаску, но не более 0,5мм.
Вообще-то, в слесарном деле есть такая операция — притупление острых кромок. Это когда серьёзные требования к изделию предъявлять не обязательно, но товарный вид желательно создать.
Балеринка вещь хорошая, но она больше подходит для вырезания различных прокладок из листового материала (паранит, резина, кожа и т.д.). А отверстия лучше и быстрее всего вырезать корончатой фрезой, наборы которых сейчас уже есть в продаже (диаметры разные). Этими фрезами можно вырезать отверстия даже в металле (я вырезаю горловины бензобака), и причём очень удобно работать, когда поверхность неровная, то есть цилиндрическая труба, как в вашем случае (балеринка в таком случае работает рывками — ведь поверхность трубы не ровная). А корпус из полипропиленовой трубы — это классная идея. Спасибо.
Олег, первоначально эта балеринка была изготовлена именно для вырезания отверстий в металле под ламповые панели (писал в статье). Тогда ещё не было транзисторов, а тем более корончатых фрез.
Предложенный вами способ имеет один большой недостаток — фиксированный размер этих самых фрез, что не позволит вырезать отверстия произвольного диаметра.
Для отверстий до 30 мм (и даже чуть больше) в листовом материале есть конические и ступенчатые свёрла. Они дорого стоят… но они того стоят! Зажимаются в обычный шуруповёрт, практически никакого усилия при сверлении и качество отверстий близко к идеалу.