Замена набоек, с сохранением фабричного стыковочного узла, своими руками.
Замена набоек, с сохранением фабричного стыковочного узла, своими руками.
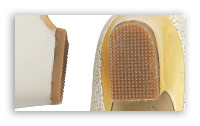
В статье рассказано о технологии изготовлении набоек для дамских туфель, сохраняющих функцию оригинального стыковочного узла. Речь идёт о набойках, крепящихся стальными фиксаторами.
Самые интересные ролики на Youtube
![]() |
![]() |
![]() |
![]() |
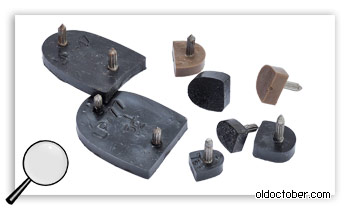
Каблуки дамских туфель часто снабжены сменными пластиковыми набойками, которые крепятся к каблукам стальными фиксаторами.
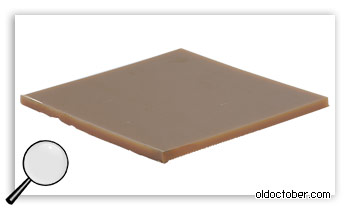
Обычно, при износе таких набоек, сапожники заменяют их набойками, изготовленными из листового полиуретана. Набойки эти сначала подклеивают клеем "Наирит или "Десмакол", а затем прибивают гвоздями к каблукам. Я тоже купил за 2,2$ кусок полиуретанового листа, а за 0,6$ тюбик Наирита, но идти проторённым путём мне было скучно. Последнее и послужило стимулом к разработке оригинальной технологии.
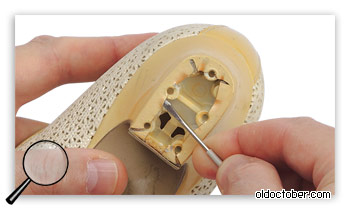
Недостаток традиционного метода ремонта заключается в том, что при замене набоек, их приклеивают не только к каблуку, но и к краям материала, обтягивающего каблук. При очередной замене набоек, покрытие каблуков может быть повреждено. Да и такую замену невозможно произвести без специальных материалов и инструментов. Ведь фабричный стыковочный узел сапожники просто игнорируют, и в лучшем случае, забивают в его отверстия деревянные чопики.
Замена же набоек, по предложенной ниже технологии, позволит вернуть обувь к жизни с сохранением функциональности фабричного стыковочного узла.
Конечно, никакой сапожник не станет усложнять себе жизнь ради того, чтобы сохранить ремонтопригодность обуви на фабричном уровне. Но, самодельщика эта технология может заинтересовать, особенно, если он решится потягаться с местным сапожником в мастерстве или угодить своей даме.
Как уже повелось – видео для тех, кому некогда читать.
Длительность основной части ролика чуть более 6-ти минут. Формат Full HD.
Описание технологии изготовления набоек

Суть технологии заключается в том, что фиксаторы сначала вплавляются в полиуретан с помощью оправок поз.1 и поз. 2, а потом место крепления каждого фиксатора армируется медной оплёткой от экранированного провода c помощью оправки поз.3.
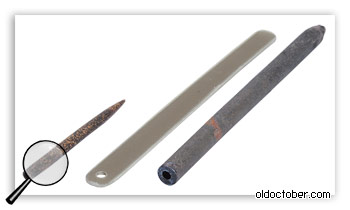
Это те же оправки в натуральном виде. Цилиндрические оправки изготовлены из жал от паяльников, диаметром 6 и 8 мм. Плоская оправка вырезана из стеклотекстолита толщиной 1,5мм. Если, при изготовлении оправок, использовать обратную сторону жала, то функциональность жал не пострадает.
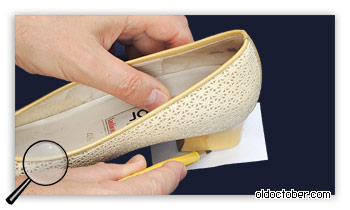
Для переноса размеров стыковочного узла используем шаблон из бумаги, закреплённый на каблуке с помощью двухстороннего скотча.
Сначала обводим каблук по периметру карандашом.
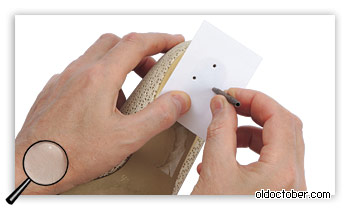
Затем протыкаем бумагу в местах расположения отверстий фиксаторов с помощью любого подходящего предмета конической формы.
Для каждой туфли нужно изготовить индивидуальный шаблон.
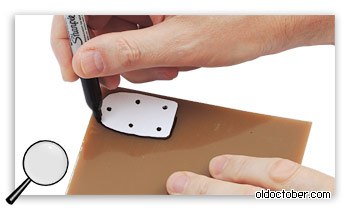
Размечаем по шаблону контур заготовки и отверстия для фиксаторов с помощью фломастера.
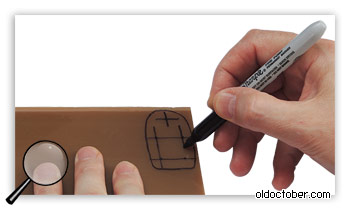
Добавляем осевые лини в места расположения фиксаторов для уверенного позиционирования последних в будущем.
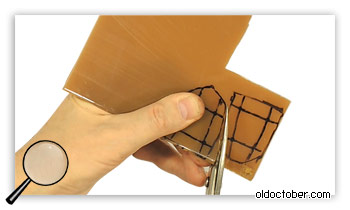
Вырезаем заготовки по шаблону с небольшим запасом на обработку. Сделать это можно ножом, и я это пробовал. Но, ножницами резать полиуретан оказалось намного проще и быстрее.
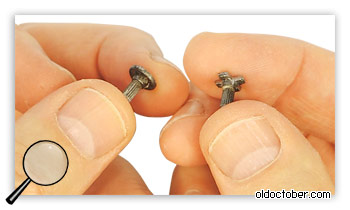
Многие фиксаторы, которые мне попадались, уже имели крестообразную шляпку. Но, если вам попадутся фиксаторы с круглой шляпкой, то такие шляпки придётся доработать с помощью надфиля.
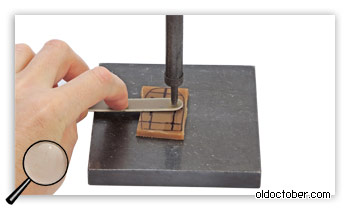
При вплавлении фиксаторов, нужно иметь в виду, что температура плавления полиуретанов лежит в диапазоне 160 - 220°С. Температура жала паяльника, при этом, должна быть 300°С и более, чтобы процесс погружения фиксаторов в заготовку был быстрым. Длительный нагрев полиуретана может снизить прочность соединения.
Для улучшения передачи тепла от оправки к фиксатору, полость оправки нужно на 1/3 заполнить припоем.
Стеклотекстолитовая пластинка с отверстием обеспечит заполнение пустот, образовавшихся во время вплавления фиксаторов в заготовку.
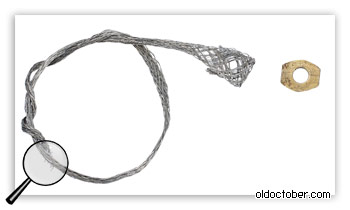
Армирование производим с помощью снятой с экранированного провода медной оплётки и латунной или стальной шайбы.
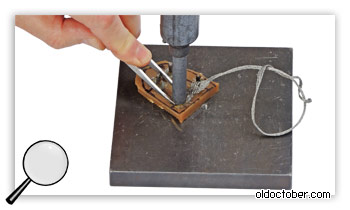
Складываем оплётку вдвое, если переплетение проводков редкое, и нанизываем её на фиксатор. Поверх одеваем латунную шайбу, которую прижимаем пинцетом. Прогреваем оплётку паяльником с восьмимиллиметровой оправкой до тех пор, пока оплётка не погрузится в полиуретан. Охлаждаем соединение водой, не отпуская пинцета. Удаляем шайбу. Отрезаем излишки оплётки. Выступающие края оплётки можно вплавить в заготовку с помощью паяльника с плоским жалом.
С помощью молотка и лапы, если она имеется, фиксируем набойку на каблуке. У меня сапожной лапы нет, поэтому я использую подходящий стальной брусок.
Если обнаружилось, что фиксаторы слишком свободно вставляются в гнёзда, то можно смазать гнёзда небольшим количеством силиконовой герметики. Такое соединение позволит при необходимости демонтировать набойки, без повреждения гнёзд фиксаторов.
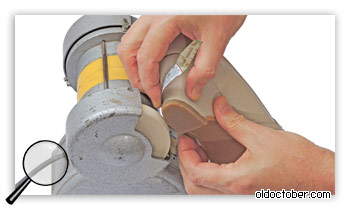
В заключение, обтачиваем набойку прямо по каблуку. Защищаем внешнюю поверхность каблука кусочком жести от консервной банки. Даже если защищённый участок каблука не просматривается, соприкосновение наждачного круга с жестью будет отчётливо слышно.
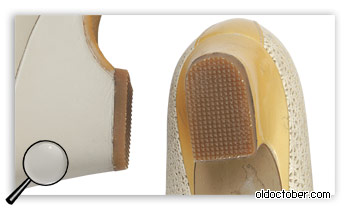
Вот что у нас получилось.
Спасибо за хороший совет. Никогда не мог понять: почему производители обуви ставят пластмассовые набойки.
Потому что пластик быстро и легко отливается на термопресс автоматах, а производство полиуретана — процесс медленный.
Чудесный сайт! admin, и всё это в одном лице? Богатый у Вас опыт.
В любом случае, с Новым годом!
Спасибо Сергей! Вас тоже с Новым годом! Здоровья и творческих успехов!
Всегда приятно прочитать или посмотреть-послушать толковые технические решения и устройства, которые может выполнить любой мужик с прямыми руками! Чувствуется у Вас богаты инженерный опыт. Чертежи, детализация, порядок выполнения и «узкие места» при изготовлении… Ностальгия… Как хороший журнал юный техник или ему подобный посмотрел. Выражаю своё восхищение и глубокое уважение в Вашему творчеству, не останавливайтесь!
Спасибо Владимир за отзыв! Но, в следующий раз, лучше покритикуйте или укажите на ошибки. Это полезнее.